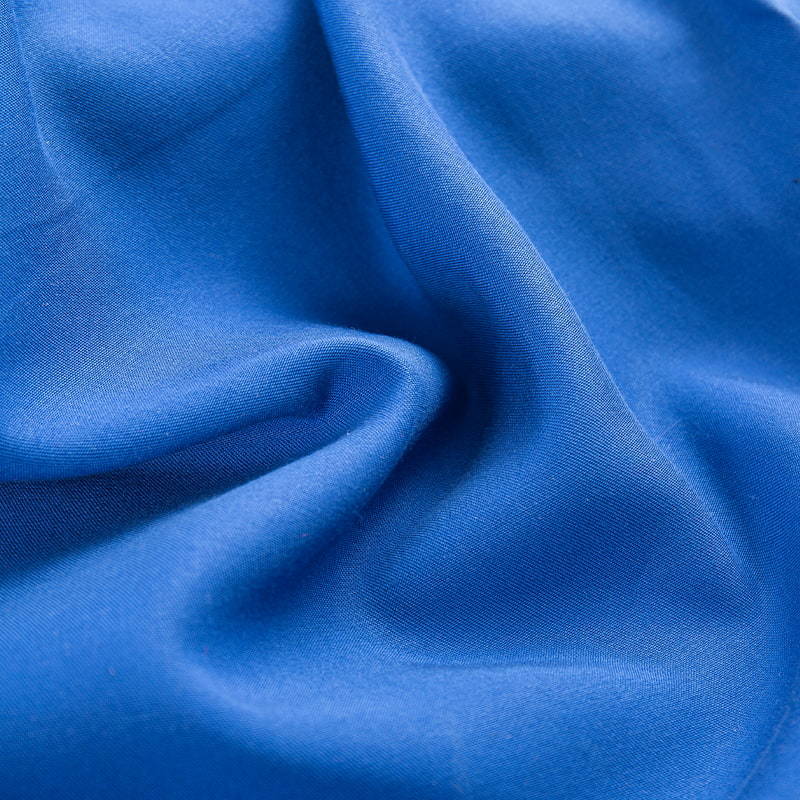
Conductive fiber series fabrics comprehensive knowledge analysis: Buyers must read guide!
In today's era of deep integration of technology and materials, conductive fiber series fabrics have moved from the laboratory to a broad application stage. Whether pursuing functionality, safety, or embracing the wave of intelligence, conductive fiber fabrics play an increasingly important role. For buyers, a deep understanding of the full picture of this type of special fabric is the key to making wise purchasing decisions. This guide aims to systematically sort out all the core knowledge points that buyers may involve when searching, evaluating, purchasing and using conductive fiber fabrics, covering from basic principles to cutting-edge applications, from performance indicators to market considerations.
Part I: Basic cognition - What are conductive fibers and conductive fabrics?
1. The core definition of conductive fiber:
•The most basic question: What exactly is conductive fiber? What is the essential difference between it and ordinary textile fibers?
•Core characteristics: Fiber materials that can conduct electric current or electromagnetic waves have much higher conductivity than conventional polyester, cotton, wool, etc.
•Material composition: Understand the diversity of its conductivity sources (metal itself, metal plating, carbon-based materials, conductive polymers, etc.).
Morphological structure: Understand how the microstructure of fibers affects conductivity (solid, core-wrapped, coated, composite structure, etc.).
2. Composition and form of conductive fabrics:
•From fiber to fabric: How are conductive fibers integrated into the final fabric? Is it as a main component or auxiliary material?
Main forms:
•Woven conductive fabrics: Conductive yarns are interwoven through warp and weft to form cloth, with a stable structure and relatively clear and controllable conductive paths.
•Knitted conductive fabrics: Conductive yarns are interlocked through coils to form fabrics, with good elasticity and high fit, suitable for occasions requiring dynamic stretching.
•Non-woven conductive fabrics: Conductive fibers are reinforced into cloth by mechanical, thermal bonding or chemical methods, with low cost and many filtering and shielding applications.
•Coated/laminated conductive fabrics: Conductive coatings (such as conductive silver paste, conductive glue) or laminated conductive films (such as metal foil, conductive non-woven fabrics) are applied to ordinary base fabrics, and the conductive layer is located on the surface.
•Composite structure: Understand the design concept of multi-layer composite conductive fabrics (such as wear-resistant outer layer, conductive middle layer, and comfortable inner layer).
3. Popular interpretation of the principle of conductivity:
•Charge carrier: What "carries" charge inside the material? (Electrons, ions)
•Resistance concept: Why is conductivity measured by resistance (or conductivity)? The difference between surface resistance and volume resistance?
•Key factors affecting conductivity: The conductivity of the fiber itself, the distribution density of the fiber in the fabric, the number and quality of contact points, ambient temperature and humidity, etc.
•Electromagnetic shielding principle: How do conductive fabrics reflect and absorb electromagnetic waves? What is the relationship with conductivity?
Part II: Material Spectrum - Family Members of Conductive Fibers
4. Metal-based Conductive Fibers:
•Pure Metal Fibers: Stainless Steel Fibers are the most typical representatives. Features: high conductivity, high strength, high temperature resistance, corrosion resistance, relatively high cost, hard feel, easy to break. Main application areas: high-end electromagnetic shielding, antistatic, high-temperature filtration.
•Metal-plated Fibers:
•Silver-plated Fibers: King Status. Ultra-high conductivity and electromagnetic shielding effectiveness (SE), excellent antibacterial properties, but high cost, oxidation resistance and repeated washing resistance need attention. Widely used in high-end medical electrodes, smart clothing, and military shielding.
•Copper/Nickel-plated Fibers: The cost is lower than silver plating, with good conductivity and good shielding effectiveness. Copper plating is easy to oxidize (discoloration), and nickel plating needs attention for biocompatibility. Commonly used in general shielding and antistatic tooling.
•Other metal plating: Such as gold plating (special use, extremely high cost), alloy plating (seeking performance balance), etc.
•Metal compound fibers: Such as tin oxide and indium tin oxide (ITO) coated fibers, which have certain conductivity and transparency, but are brittle, poor bending resistance, and limited application.
5. Carbon-based conductive fibers:
•Carbon black composite fibers: Conductive carbon black particles are mixed into a polymer (such as polyester, nylon) matrix and spun. Low cost, mostly black/gray in color, medium conductivity, and good washing resistance. It is the main force in anti-static applications (such as workwear, carpets, conveyor belts).
•Carbon nanotube (CNT) fibers/modified fibers:
•Great potential: extremely high theoretical conductivity, good strength, and light weight. Spin CNT directly or disperse it into a polymer matrix.
•Challenges: Large-scale uniform dispersion, spinning difficulty at high concentrations, and high costs. It is a hot direction for smart textiles and high-performance composite materials.
•Graphene fibers/modified fibers: Similar to CNT, it has the characteristics of ultra-thinness, high conductivity and thermal conductivity. The preparation process is complex and the cost is extremely high, and commercial applications are in the early exploration stage.
•Active carbon fiber: Mainly uses its adsorption, conductivity is its additional characteristic, usually not high. Used for special filtration or electrodes.
6. Intrinsically conductive polymer (ICP) fiber:
•Representative materials: polyaniline (PANI), polypyrrole (PPy), polythiophene (PEDOT:PSS).
•Features: The material itself is conductive (no need to add fillers), the performance can be adjusted through molecular design, good flexibility, adjustable color (PANI can be green or blue).
•Challenges: Environmental stability (easy to oxidize and degrade), some materials have poor solubility/processability, conductivity is usually lower than metal series, and washability needs to be improved. It has unique advantages in sensors, flexible electrodes, and stealth materials.
7. Composite/hybrid conductive fiber:
•Design idea: Combine the advantages of different materials and learn from each other. For example:
Polyester/nylon as the core, metal-plated on the surface (improve the feel and reduce costs).
Metal fiber and ordinary fiber blending (balance conductivity, cost, comfort).
Carbon material and metal material composite (improve conductivity and reduce costs).
•Market mainstream: Many commercial conductive fibers belong to this category to meet specific performance-price ratio requirements.
Part III: Performance Vertical and Horizontal - Key Indicators for Measuring Conductive Fabrics
8. Conductive Performance - The Core of the Core:
•Surface Resistance (Rs): The most commonly used indicator! The unit is ohm (Ω) or ohm/□ (square resistance). The lower the value, the better the conductivity. Buyers need to clarify the specific resistance range required for the target application (for example: antistatic is usually 10^4 - 10^9 Ω/□, and efficient shielding may require <1 Ω/□).
•Volume Resistance (Rv) and Resistivity (ρ): More reflective of the conductivity of the material itself, the test is relatively complex, and is more commonly used in fibers and homogeneous materials.
•Conductivity (σ): The reciprocal of resistivity, a direct measure of the material's ability to conduct current.
•Test Standards and Methods: Understand common standards (such as ASTM D257, EN 1149, GB/T 12703, ISO 3915) and test equipment (such as four-probe resistance tester, concentric ring electrode). Ambient temperature and humidity have a significant impact on test results!
9. EMI Shielding Effectiveness (SE):
•Definition: The material's ability to attenuate incident electromagnetic waves, in decibels (dB). The higher the value, the better the shielding effect (e.g. 30dB attenuates 99.9%, 60dB attenuates 99.9999%).
•Frequency range: Shielding effectiveness varies with the frequency of the electromagnetic wave! Buyers must clearly understand the frequency range that needs to be shielded (e.g. mobile phone band, WiFi, radar waves, power frequency).
•Test standards and methods: Understand common standards (e.g. ASTM D4935, EN 61000-4-21, GB/T 30142) and test environments (far field/near field, plane wave/microwave darkroom). SE is closely related to conductivity, but it is not a simple linear relationship. It is also affected by material thickness, layer structure, and incident wave type.
10. Antistatic performance:
•Purpose: To prevent the accumulation and sudden release of static charge (ESD).
•Key indicators: static voltage half-life (the time required for the charge to decay to half of the initial value), in seconds. The shorter the time, the better (such as the national standard requires <60s or shorter). Surface resistance is also an important reference.
•Test standards: such as GB/T 12703, ISO 18080, AATCC 76.
11. Physical and mechanical properties:
•Strength and wear resistance: Is the fabric strong and durable enough? Especially for workwear, protective clothing, and frequently used electrodes.
Elongation and elasticity: It is crucial for applications that require close-fitting wear or dynamic activities (such as smart clothing, sports monitoring).
•Feel and drape: Affects wearing comfort and the appearance texture of the final product. Metal fibers are hard, carbon black fibers are dark in color, and silver-plated fibers are relatively soft but costly.
•Thickness and weight: Affects the thinness, flexibility and cost of the product.
12. Environmental tolerance and durability:
•Washability: How many standard washes can the conductive performance withstand without significant decline? This is a hard indicator for evaluating the life and practicality of fabrics! Test standards (such as AATCC 135, ISO 6330). The washability of different conductive fibers varies greatly (silver plating requires special processes to improve).
•Friction resistance: Will the surface conductive layer or fiber fall off or fail under repeated friction?
•Weather resistance: Resistance to ultraviolet rays, temperature changes, and humid environments. Metal fibers have good weather resistance, and ICP is prone to aging.
•Chemical resistance: Is it in contact with sweat, disinfectants, solvents, etc.? Corrosion resistance and chemical stability need to be considered (such as stainless steel has good acid and alkali resistance, and copper is easy to oxidize).
13. Safety and biocompatibility:
•Skin contact safety: Will it cause allergies (such as nickel release must comply with REACH and other regulations)? How is the biocompatibility (especially medical electrodes)?
•Heavy metal content: Metal-based fibers need to pay attention to whether harmful heavy metals such as lead and cadmium exceed the standard.
•Flame retardancy: Flame-retardant conductive fabrics may be required for specific application scenarios (such as aviation and electronic workshops).
14. Processing performance:
•Cutting and sewing: Is the conductive yarn easy to break? Is the conductive layer easy to peel off? Are special needles or processes required?
•Hot pressing/bonding: Can the electrodes or integrated electronic components withstand hot pressing or use of hot melt adhesive?
•Dyeing and finishing: Carbon black fiber is difficult to dye, metal fiber has poor dyeability, and silver-plated fiber needs to be dyed at low temperature. Do finishing additives affect conductivity?
Part IIII: Application fields - the stage for conductive fabrics to show their talents
15. Smart clothing and wearable technology:
•Physiological signal monitoring: As electrodes or sensor elements to collect ECG, EMG, EEG and other signals. High conductivity, low contact impedance, comfortable fit, sweat resistance and washability are required.
•Sports performance analysis: Monitoring muscle activity, breathing, posture, etc.
•Heating clothing: Using conductive fibers to generate electricity and heat (such as ski suits, medical protective gear). Resistance uniformity, heating efficiency, and safety protection circuits need to be considered.
•Human-computer interaction: Integrated on clothing as a touch sensing or gesture recognition interface.
•Data/energy transmission: Explore the use of conductive yarns as flexible wires to connect sensors, chips, and batteries.
16. Medical and health care:
•Medical electrodes: ECG monitoring patches, defibrillator electrodes, TENS therapy electrodes, etc. Core requirements: biocompatibility, low polarization impedance, stable conductivity, adhesion, breathability, and comfort (long-term wear). Silver-plated fabrics are an important choice.
•Functional medical textiles: antistatic surgical gowns/curtains (to prevent dust absorption and reduce the risk of electric sparks), electromagnetic shielding ward curtains/clothing (to protect sensitive equipment or special patients), antibacterial dressings (using silver ions), and pressure/strain sensing bandages for rehabilitation.
•Remote health monitoring: The core component of wearable monitoring equipment at home.
17. Protection and safety equipment:
•Antistatic (ESD) protection: work clothes, gloves, wristbands, and equipment covers in dust-free workshops in the electronics industry; explosion-proof work clothes in the petrochemical industry; clothing for flammable and explosive material operation sites. Reliable and lasting charge dissipation capabilities are required.
•Electromagnetic radiation (EMR) protection: radiation protection clothing for pregnant women, protective clothing for special types of work (radar stations, near high-voltage lines), shielding tents/curtains, and electronic equipment shielding covers (such as mobile phone bags and computer bag linings). The shielding frequency and efficiency requirements need to be clarified.
•Military and defense: electromagnetic shielding tents/command posts, stealth materials (radar absorbing), explosion-proof clothing (combined with other materials), anti-interference communication equipment, soldiers' physiological status monitoring clothing.
18. Industrial and technical fields:
•Industrial sensors: Flexible sensor substrates or electrodes for monitoring pressure, deformation, temperature, humidity, etc.
•Static dissipation: Conveyor belts, filter bags, powder handling equipment linings, aircraft fuel tank components (anti-static sparks).
•Electromagnetic compatibility (EMC): Internal shielding pads for electronic equipment, shielded cable braids, shielded chassis gap materials (conductive cloth pads).
•Grounding and discharge: Grounding straps and discharge brushes for special purposes.
•Energy: Fuel cell electrode substrate materials, supercapacitor electrode materials (under exploration).
19. Home and special textiles:
•Home textiles: Antistatic carpets, curtains, bedding (reduce dust absorption and improve comfort), electric blankets/heating wires for floor heating.
•Automotive interior: Antistatic seat covers, steering wheel covers, interior fabrics; used for seat heating and sensor integration.
•Filter material: Conductive non-woven fabric is used for industrial dust removal (preventing static adsorption, improving filtration efficiency, and facilitating dust removal).
•Art and design: Used for creative clothing and interactive installation art.
Part V: Procurement and Supply Chain - Buyers' Practical Considerations
20. Clear requirements and specification definitions:
•Core functions: What is the top priority? Is it strong conductivity/low resistance? High shielding effectiveness? Reliable antistatic? Or as a comfortable electrode? The target performance indicators must be quantified (resistance range, SE value, half-life).
•Application scenarios: Environment (temperature and humidity, chemical contact), usage (skin-friendly? Dynamic? Washing frequency?), life requirements.
•Physical requirements: Fabric structure (woven/knitted/non-woven), thickness, weight, color, feel, strength, elasticity, etc.
•Regulations and standards: Industry standards (medical, military, electronics), safety and environmental regulations (REACH, RoHS, OEKO-TEX®, etc.).
21. Supplier evaluation and selection:
•Technical strength: Do you have material research and development capabilities? Is the production process mature and stable? Can you provide customized solutions?
•Quality control: Is there a complete quality management system? Are the testing equipment complete? How is the batch stability?
Production scale and delivery time: Can the purchase volume and delivery time requirements be met?
•Cost and quotation: The cost of different materials and technical routes varies greatly (silver plating vs. carbon black). Understand the cost structure (raw materials, process complexity, batch size).
•Sample evaluation: Be sure to request samples for rigorous performance testing (resistance, shielding, washability, etc.) and actual application simulation!
•Industry reputation and cases: Are there any successful application cases? How are the customer reviews?
22. Cost structure and optimization strategy:
•Raw material cost: Metal (silver, copper, stainless steel), carbon material (carbon black, CNT, graphene), polymer matrix cost.
•Production process cost: Spinning (especially composite spinning), plating process (electroplating, chemical plating, vacuum plating), coating process, weaving/knitting/non-woven molding process complexity and energy consumption.
•Performance premium: High performance (such as ultra-high conductivity, high SE, ultra-thin, ultra-washability) will inevitably bring high costs.
•Optimization ideas:
Accurately match the needs and avoid over-design (just enough).
Consider mixed use (high-performance conductive fibers for key parts and low-cost fibers for other parts).
Explore cost-effective materials (such as improved carbon black composites and copper-nickel plating).
Large-scale procurement reduces costs.
Work with suppliers to develop customized solutions that meet specific needs.
23. Market trends and cutting-edge technologies:
•Intelligence and integration: Conductive fabrics are becoming increasingly important as a "flexible interconnection platform" for wearable electronic systems, requiring seamless integration with sensors, chips, and power supplies.
•High performance and multifunctionality: Pursue higher conductivity/SE, better washability/durability, and have multiple functions such as antibacterial, temperature control, and sensing.
•Comfort and aesthetics: Improve the rigidity, thickness, and single color (especially carbon black) of traditional conductive fabrics to make them closer to ordinary fabrics.
•Sustainability: Pay attention to the environmental protection of material sources (such as reducing the use of heavy metals), the greening of the production process, and the recyclability of products. Bio-based conductive materials are the direction of exploration.
•New material breakthroughs: Commercialization progress of CNT fibers, graphene fibers, and high-performance ICP fibers and their potential impact on the market structure.
•Advanced manufacturing technology: Application of 3D printed conductive structures and nanofiber electrospinning technology in the preparation of high-performance conductive networks.
Part VI: Common Problems and Countermeasures (Buyer's Perspective)
24. Will the conductivity decay? How to maintain it?
•Definitely! Main factors: washing wear, mechanical friction, oxidation corrosion (metal), environmental aging (ICP).
•Countermeasures: Select materials and processes with good washability/wear resistance/weather resistance; optimize product design to reduce friction areas; provide instructions for use and maintenance (such as low temperature and gentle washing, avoid bleaching agents).
25. How to test and verify the performance data provided by suppliers?
•Independent third-party testing: For key projects or large-volume purchases, send to authoritative testing agencies for retesting according to standards.
•Establish internal testing capabilities: Purchase basic resistance testers and other equipment to conduct random inspections on each batch of incoming materials.
•Simulate actual application testing: Make fabrics into sample pieces (such as small electrodes, shielding bags) for functional testing.
26. How to choose different conductive materials?
•Ultra-high conductivity/shielding: Silver-plated fiber/fabric, pure metal fiber blended fabric (high cost)
•Reliable antistatic/general shielding/cost sensitive: carbon black composite fiber/fabric, copper-nickel-plated fiber/fabric.
•Comfortable electrode/flexible sensing: silver-plated knitted fabric, high-performance ICP coated fabric (washability needs to be evaluated), carbon-based fabric with special structure.
•High temperature/corrosion resistance: stainless steel fiber fabric.
•Transparent conductivity: ITO coated fabric (high brittleness), metal grid (discontinuous), flexible transparent conductive materials under exploration (such as silver nanowires, conductive polymers).
27. Can conductive fabrics be dyed?
•Metal fiber/plated fiber: It is difficult to dye, usually retaining the original color of the metal (silver white, copper gold, stainless steel gray), or dyeing the base fabric (in the case of core-wrapped structure).
•Carbon black composite fiber: The color is dark (black/gray), and it is extremely difficult to dye into bright colors.
•ICP fiber: Some can be dyed (such as polyaniline can be green/blue), but the color range is limited.
•Coated/laminated fabric: Mainly dye the base fabric, and the color of the conductive layer is difficult to change.
Buyers need to clarify the color requirements and communicate with suppliers about the feasibility.
28. Is small batch customization feasible? What is the cost?
It is feasible, but the cost is usually much higher than that of standard products. It involves mold opening fees, sample fees, and high losses in small batch production.
•Communication points: clarify the minimum order quantity (MOQ); understand the cost structure of customization; evaluate whether customization is really necessary (can the modification of standard products meet it?).
29. How to integrate conductive fabrics into the final product?
•Connection issues: How to reliably connect wires or circuits to conductive fabrics? Common methods: conductive adhesive bonding, riveting/snap connection, hot pressing welding (the fabric needs to be heat-resistant), and sewing conductive wires.
•Circuit design: Design of conductive paths (wiring), insulation treatment (to prevent short circuits), impedance matching (especially for high-frequency signals).
•Suggestions: Seek support from suppliers or design teams with experience in electronic textile integration; conduct sufficient prototype testing.
Part VII: Future Outlook - Infinite Possibilities of Conductive Fabrics
30. Integration and Innovation:
•Combined with Artificial Intelligence (AI): Conductive fabrics collect massive amounts of physiological/environmental data, and use AI analysis to achieve more accurate health assessments, personalized services, and motion recognition.
•Integration with the Internet of Things (IoT): Conductive fabrics serve as the sensing and transmission layer of smart clothing/equipment, and seamlessly connect to the Internet of Things.
•Combined with energy harvesting technology: Explore the use of human motion, body temperature differences, etc. to power wearable devices through conductive fabrics.
•New sensing functions: Develop multifunctional smart conductive fabrics that can simultaneously sense pressure, humidity, temperature, chemicals, etc.
31. Challenges and breakthrough directions:
•Durability and reliability: Continuously improving the ability to withstand repeated washing, friction, bending, and environmental aging is the key bottleneck for expanding applications.
•Cost control for large-scale production: Promote the scale-up of cost reduction of high-performance materials (such as CNT, graphene) and advanced processes.
•Standardization and testing methods: As applications become more complex, more complete performance testing standards and evaluation systems that are more in line with actual application scenarios are needed.
•Recycling and Sustainability: Solve the recycling challenges of composite materials (metal/polymer, carbon/polymer) and develop more environmentally friendly alternative materials.